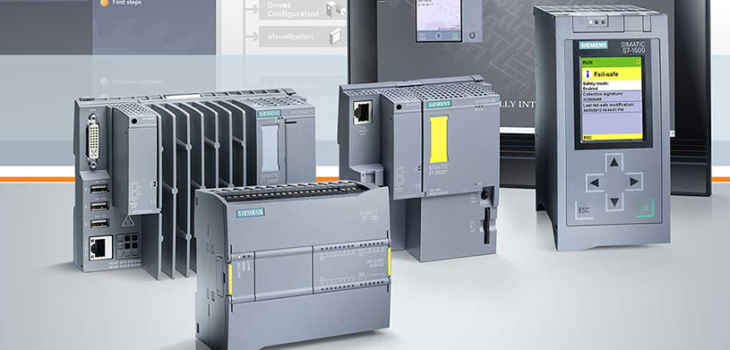
10 aspectos a la hora de seleccionar un PLC…
La seguridad es un aspecto crucial a la hora de diseñar una nueva máquina o línea de fabricación, saber seleccionar el sistema de control de seguridad corercto para monitorear todos sus dispositivos de protección es un aspecto muy importante.
Omron ha publicado 10 aspectos a tener en cuenta a la hora de elegir el PLC de Seguridad correcto para cada aplicación ¿Cómo elige el controlador correcto?
1 – Número de dispositivos de E/S
Una buena forma de comenzar es determinar el número y los tipos de dispositivos de entrada y salida que se deben conectar al controlador. Con las salidas, debe determinar si se requiere retroalimentación y si cada salida necesita ser monitoreada individualmente. (Esto puede aumentar el número de entradas requeridas.)
2 – Conectividad de E/S de seguridad
También debe considerar el tipo de conexión necesaria. Según el controlador utilizado y la clasificación de peligro, el número de dispositivos que se pueden conectar a una tarjeta de entrada o el controlador en sí puede variar.
3 – E/S estándar
Otra consideración de E/S es la necesidad de conectar dispositivos de entrada e indicación u otros tipos de dispositivos de salida que no requieran señales relacionadas con la seguridad.
4 – Velocidad
Este aspecto es muy importante al seleccionar una plataforma de seguridad, tanto desde el punto de vista del rendimiento como del costo. Los tiempos de respuesta más rápidos significan que los dispositivos como las barredas de seguridad pueden montarse más cerca del peligro. Preste atención a la velocidad del sistema para garantizar que la seguridad no se vea comprometida al cambiar los controladores de seguridad.
5 – Monitorización
Es posible que los controladores y sistemas programables más pequeños no requieran monitorización por parte de un PLC, HMI u otro dispositivo de red, pero en sistemas más grandes es imprescindible saber qué dispositivo está encendido, apagado o tiene un error.
6 – Acceso a los datos de estado
La monitorización proporciona una excelente herramienta para el funcionamiento general, pero los datos deben ser fácilmente accesibles. Los protocolos serie requieren que los puntos del programa se asignen a bits específicos que intercambian información con entradas y salidas en otro dispositivo. El mapeo de esta información debe ser rastreado y documentado, lo que puede ser engorroso y llevar mucho tiempo. Algunos sistemas tienen la capacidad de asignar toda la información de estado del controlador de seguridad directamente al PLC. Estos sistemas son fáciles de usar y se puede acceder fácilmente a grandes cantidades de datos.
7 – Espacio en el armario de control
Esta es una gran ventaja de un sistema programable, ya que las unidades de entrada del controlador ofrecen una mayor densidad en un paquete mucho más pequeño (puede ahorrar hasta un 25 por ciento de espacio).
8 – Complejidad
La creación de sistemas de seguridad complejos con varios modos de operación segura, diferentes categorías de paradas y otras funciones más avanzadas era difícil de realizar con circuitos cableados, y con frecuencia involucraba costosas unidades especializadas. Los circuitos de parada de categoría 1 que usan unidades de relé de retardo de tiempo son complejos para el cableado y su funcionamiento es limitado, pero con los sistemas programables de hoy en día, algunos bloques de funciones pueden configurarse en el software y consumir menos espacio en el panel de control. Los controladores programables pueden mejorar las capacidades de monitorización en configuraciones complejas, haciéndolos más seguros y fáciles de configurar.
9 – Estilo de programación
Hay muchos estilos diferentes de programación que incluyen ladder, bloques de funciones con arquitecturas fijas y flexibles y varios otros estilos. Muchos fabricantes han adoptado recientemente una arquitectura abierta, que permite una comprensión más fácil de los diferentes sistemas de los proveedores y permite tiempos de desarrollo más cortos si se necesitan sistemas alternativos.
10 – Escalabilidad
Muchos fabricantes de equipos requieren una arquitectura escalable en cierta medida, desde equipos independientes más pequeños hasta líneas de producción completas. La capacidad de reutilizar hardware y programas y aprender un estilo de programación mejora la productividad.
Fuente: Automation OMRON