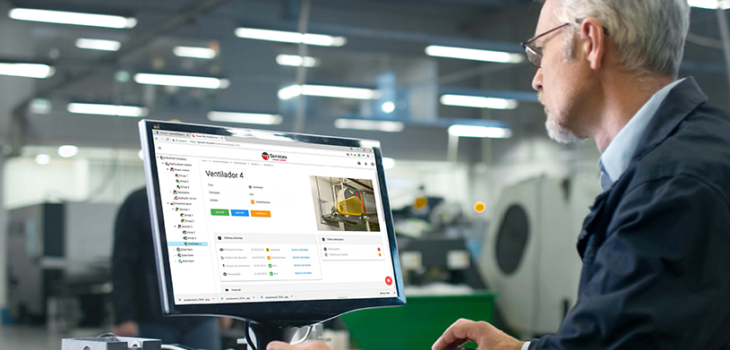
5 problemas que ocurren durante la implantación de un…
1. Formación deficiente de técnicos y operarios
Lo primero es revisar el perfil de los técnicos y operarios. Una vez que el director de producción y mantenimiento ha llegado a la decisión de implantar un plan de mantenimiento predictivo, debe ver si sus empleados son capaces de llevar a cabo las tareas necesarias, ya que probablemente no tengan el perfil ni la formación correcta.
“Si desea mejorar los conocimientos de tu equipo de técnicos, debes ofrecerles formación sobre las herramientas a implementar, utilizando las nuevas tecnologías de mantenimiento predictivo industrial que mejoran tus máquinas e instalaciones, porque tienes que tener presente que cuanto más sepan sobre la tecnología, más partido sacará del sistema de medición día a día.”
Con la formación, buscas que tus técnicos comprendan que es necesario monitorizar, alinear, equilibrar y lubricar las máquinas para garantizar una alta fiabilidad operativa y conozcan los distintos métodos de monitorización, alineación, equilibrado y lubricación que pueden aplicar en los casos particulares de tus instalaciones.
2. No invertir en las herramientas y equipos adecuados
3. Baja eficacia y eficiencia en la realización de los trabajos de mantenimiento predictivo
Para mejorar estos dos puntos, hay que elaborar un plan de optimización y análisis de criticidad del parque de máquinas y la instalación al completo. Para ello hay que:
- Revisar los históricos para saber la recurrencia y probabilidad de fallos.
- Analizar los costes que se han producido por estos fallos dentro del proceso productivo, tanto costes operativos como los costes directos de mantenimiento.
- Hacer un plan al detalle sobre qué máquinas comenzar la implantación. Hay que saber bien sobre qué máquinas invertir los recursos para poder ser eficaz y eficiente.
4. Actuar en el síntoma y no en la causa
Una vez tengas el diagnostico de una máquina, debes actuar en consecuencia. Muchas veces nos encontramos con directores de producción con planes maravillosos de mantenimiento, pero que no ejecutan las actividades o no hacen las revisiones que dicta el plan.
Se equivocan al pensar que es una herramienta para llenar un expediente y no lo utilizan como una herramienta para conseguir un beneficio real para el negocio de la compañía. Se debe ser consecuente y se debe realizar un análisis más profundo de los resultados, es decir, no sólo debes limitarte a medir, sino que debes actuar.
Debes coger la información y analizar dónde están los fallos recurrentes y cuáles son sus causas para así poder optimizar en el medio-largo plazo la operación de la máquina.
Un caso particular que puede resultar interesante comentar es el de una máquina papelera en la cual existía un fallo recurrente que se venía repitiendo durante 20 años. Se trataba del sobrecalentamiento de unos cojinetes anti-fricción. La solución de esta empresa era cambiar los cojinetes anti-fricción cada vez que fallaban.
Sin embargo, nadie en la planta se había detenido a pensar por qué esto sucedía, hasta que se implanto un programa de análisis de causa-raíz de la situación, llegando a la conclusión que el problema era que el sistema de lubricación era deficiente. Una vez se empezó a actuar sobre este punto, los problemas de sobrecalentamiento desaparecieron.
“Si los operarios solamente actúan en el síntoma y no en la causa, los programas de mantenimiento predictivo no son eficaces.”
5. No se acompaña el mantenimiento predictivo con indicadores de gestión
Si no cuentas con indicadores de gestión, no puedes saber si está mejorando y en cuánto. Es decir, no puedes saber cuál ha sido el avance del programa. No sabes si estás mejorando en cuanto al número de fallos, no sabes si has optimizado la gestión de compra de repuestos y no sabes cuántas horas de parada no planificadas se han reducido; en definitiva, no sabes dónde te encuentras. Sin indicadores, simplemente te dedicas a cumplir con unas actividades y cumplir con un expediente.
“Una de las cosas que te sugiero incluyas en tu plan de mantenimiento predictivo es establecer los criterios de éxito e indicadores de gestión. El objetivo es poner en una sola lista todos los criterios para saber cuándo será exitoso el proyecto y cómo.”
El enfoque es establecer una base de medidas de cómo se encontraba la situación de tus máquinas antes de la implantación, monitorear los resultados una vez implantado el programa, calcular la diferencia de mejora y luego realizar un informe con los datos obtenidos.