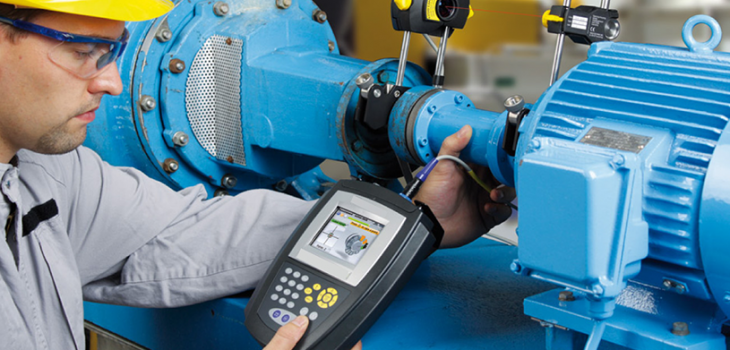
Cómo lograr ahorros de costes y energía con auditorías…
Es un hecho que las auditorías de mantenimiento predictivo ofrecen grandes ahorros de costes y energía. Puedes dar uso a estas auditorías de mantenimiento predictivo para ayudar a utilizar los recursos más eficientemente.
Por ejemplo, las auditorías de mantenimiento predictivo en plantas industriales son herramientas de evaluación poderosas que pueden ayudar a las compañías a utilizar los recursos más eficientemente y lograr objetivos específicos tales como recortar el uso de energía o reducir los gastos de sobre tiempo.
Las auditorías de mantenimiento predictivo se originaron hace dos décadas prácticamente y han crecido en popularidad de manera estable. Han encontrado uso hoy en diversas industrias que van desde manufactura y fábricas de papel hasta producción de acero y procesamiento de energía.
El proceso de auditoría puede llevar desde medio día a una semana o más en completarse. Aunque las auditorías vienen en muchas formas, se pueden clasificar generalmente en dos categorías: auditorías generales de toda la planta y auditorías específicas de pequeña escala. Las auditorías de toda la planta proveen una visión general detallada de las estrategias de mantenimiento de las instalaciones, organización, y actividades, mientras que las auditorías a pequeña escala apuntan a problemas de mantenimiento específicos como uso de lubricantes o repuestos rechazados.
Auditorías de mantenimiento generales
Las auditorías de mantenimiento generales son dirigidas usualmente por firmas consultoras u otras partes habilitadas en métodos de auditoría. La auditoría comienza típicamente con un mapeo de los procesos operacionales y los mantenimientos de activos de la instalación.
Los diagramas son producidos mostrando la estructura organizacional y diseño de la planta, incluyendo la ubicación de los talleres de mantenimiento y depósitos. Las cartas detallan los cambios de turnos y funciones del grupo de mantenimiento así como fontaneros y electricistas. La auditoría también describe la programación de mantenimiento planeado para los equipos principales. Esto incluye la frecuencia de mantenimiento previsto en máquinas clave, la cual puede ser desde mensual hasta cada tres o seis meses. Los tiempos de parada planeados para cada procedimiento también deben ser listados.
Después de que el mapeo es completado, el equipo auditor analiza la efectividad general del departamento de mantenimiento y lo compara con el de instalaciones similares y con industrias de referencia ampliamente aceptadas. Los datos de eventos de parada, disponibilidad de máquinas y tiempos extra son examinados. Finalmente, un reporte es emitido resumiendo los hallazgos de la auditoría e incluyendo recomendaciones para hacer mejoras.
Signos reveladores de una auditoría de mantenimiento
Su instalación podría beneficiarse de una auditoría de mantenimiento si ésta (la instalación) ha sido expandida en tamaño o ha sido reestructurada. Tales cambios pueden disrumpir el flujo de trabajo y afectar la entrega de servicios de mantenimiento. Otras señales de que una auditoría puede ser aconsejable incluyen:
Ruptura del sistema de órdenes de trabajo interno que gestiona las acciones de mantenimiento.
Niveles de sobre tiempo alcanzando el 10 % o más del total de horas de mantenimiento.
Rápido y reciente crecimiento del tamaño del personal de mantenimiento.
Incremento del consumo de energía comparado con operaciones similares.
Una serie de fallas de rodamientos relacionadas con prácticas de instalación deficientes.
Considere el caso hipotético de un fabricante de tamaño mediano. La compañía tiene cuatro líneas de producción, docenas de máquinas críticas, y un enorme personal de mantenimiento. Una auditoría crea un modelo detallado de las actividades de operaciones y mantenimiento de la compañía. Un cuestionario calibra las actitudes y moral de los técnicos de mantenimiento y solicita sus comentarios con respecto a las condiciones de la planta.
La auditoría descubre altos costes asociados con tiempos extra y señala un uso ineficiente de recursos de mano de obra. También señala la falta de un programa formal para identificar la causa raíz de las fallas de máquinas, dejando la mayoría de las fallas sin explicación.
El reporte final encuentra que muchos procedimientos no básicos como la reconstrucción de equipos son realizados dentro de las instalaciones por los técnicos de mantenimiento. Este reporte recomienda cambiar la mayoría de estos trabajos hacia contratistas externos, permitiendo que los técnicos se enfoquen en responsabilidades básicas. La auditoría también propone la creación de un programa de análisis de fallas para identificar las causas de las fallas y para prevenir fallas recurrentes.
Para saber más acerca de las auditorías de mantenimiento predictivo, te invitamos a ver conocer cómo las técnicas de mantenimiento predictivo superan cualquier acción preventiva, así como también la comparación entre mantenimiento proactivo y mantenimiento reactivo.