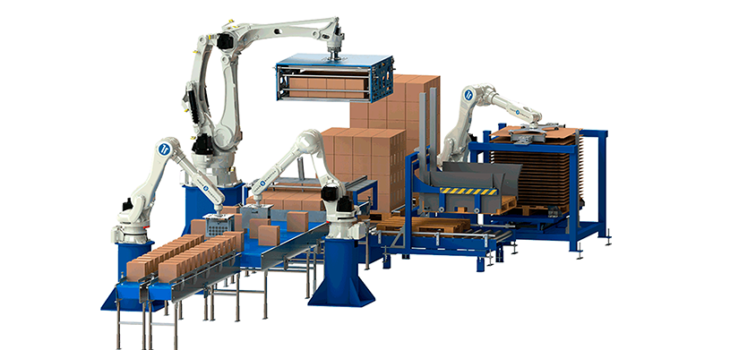
Procesos de paletizado automatizado con acopladores inductivos
Los fabricantes han estado utilizando protocolos industriales de Ethernet como su red de controles desde principios de la década de 1990. Se prefirieron los protocolos Ethernet industriales como Ethernet/IP, ProfiNet y Modbus TCP sobre los protocolos de bus de campo porque ofrecían los beneficios de un mayor ancho de banda, conectividad abierta y estandarización, todo mientras se usa el mismo hardware Ethernet que la red de TI de la oficina. Ser Ethernet estándar también le permite monitorear de forma remota dispositivos Ethernet individuales a través de la red en busca de diagnósticos y alarmas, brindando una mayor visibilidad de los datos de producción.
Con Ethernet como la tecnología clave para la Industria 4.0 y la digitalización, cada vez más dispositivos tendrán capacidades de Ethernet. Los nodos de Ethernet industriales típicos en una planta pueden incluir controladores PLC, robots, dispositivos de E/S para sensores, actuadores, medidores de flujo, transductores y colectores. Si bien es genial obtener todos los datos y diagnósticos de todo el proceso de producción, tener todos los dispositivos conectados a través de Ethernet tiene algunas desventajas. Puede conducir a redes Ethernet más grandes, lo que puede significar más costos en hardware como enrutadores, conmutadores y cables Ethernet, y algunos costos de licencia de software Ethernet se basan en la cantidad de nodos Ethernet que se utilizan en la red.
Además, a medida que se agregan más dispositivos Ethernet a una red, la propia red Ethernet puede volverse más compleja. Cada dispositivo Ethernet individual requiere una dirección IP. Si un nodo Ethernet deja de funcionar y necesita ser reemplazado, un operador necesitaría conocer la dirección IP anterior del dispositivo y tener acceso rápido al manual con instrucciones sobre cómo asignar la dirección IP anterior al nuevo dispositivo. Alguien también debe administrar las direcciones IP en la red. Deberá haber una lista de las direcciones IP en la red, así como las disponibles, de modo que cuando se agrega un nuevo dispositivo Ethernet a la red, no se utilice una dirección duplicada
Una forma de reducir la cantidad de nodos Ethernet mientras se obtienen datos y diagnósticos del dispositivo es mediante el uso de IO-Link para las comunicaciones de dispositivos de campo. IO-Link es un estándar abierto de comunicación punto a punto para sensores y actuadores publicado por la IEC (Comisión Electrotécnica Internacional) como IEC 61131-9. Como es independiente al bus de campo y al fabricante, hay una larga lista de dispositivos de fabricantes que vienen con IO-Link. Cada dispositivo IO-Link puede volver a un solo nodo Ethernet, a través de un acceso IO-Link a Ethernet. Dado que es una tecnología abierta, también hay varios fabricantes que hacen diferentes accesos de IO-Link a Ethernet industriales.
En el acceso IO-Link a Ethernet, cada canal tiene un conjunto de chips maestros IO-Link. Está diseñado para comunicarse automáticamente y proporcionar datos tan pronto como un dispositivo IO-Link se conecta a un puerto. Por lo tanto, no se requiere direccionamiento ni configuración adicional. IO-Link es punto a punto, por lo que siempre es un único dispositivo IO-Link conectado a un solo puerto en el acceso utilizando un cable de sensor estándar. Dependiendo de la cantidad de dispositivos IO-Link que se conecten a un solo nodo Ethernet, los accesos IO-Link pueden venir en 4, 8 o 16 canales de dispositivos. Este gráfico (imagen 1) muestra seis dispositivos IO-Link conectados a un único acceso Ethernet de 8 canales. Este acceso se comunica de nuevo con el controlador PLC Ethernet como una única dirección IP con un cable Ethernet estándar. Sin usar IO-Link, esto podría requerir que los seis dispositivos sean dispositivos Ethernet industriales. Cada dispositivo tendría su propia dirección IP para configurar, junto con seis cables Ethernet que regresan a un conmutador administrado de 6 puertos antes de ir al controlador PLC.