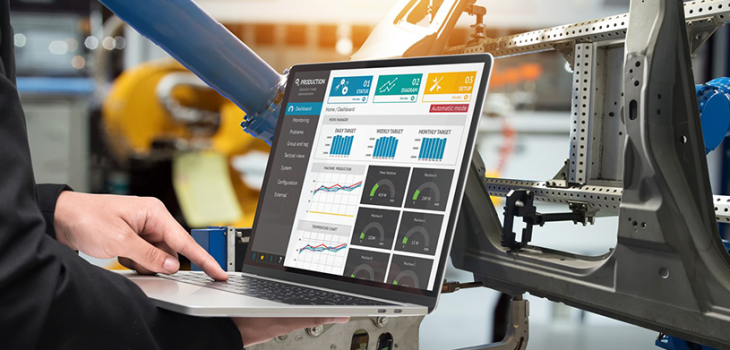
Acciones para alcanzar ahorros en tu planta
¿Qué acciones se pueden tomar para logran una mayor eficiencia en el consumo de energía de máquinas industriales y con ello ahorrar gastos? Es importante conocer y controlar las conexiones que existen entre la gestión de fiabilidad y otras responsabilidades funcionales dentro de una organización productiva, tales como la calidad y la seguridad.
Es evidente que la fiabilidad de los procesos de fabricación aumenta la calidad y es uno de los tres elementos primarios de la efectividad general del negocio. Además, cuando los procesos de fabricación son confiables y predecibles, hay menor posibilidad de que ocurra un accidente laboral.
Al hacer un pequeño análisis de gestión, se puede percibir que existe una conexión muy fuerte entre la fiabilidad y manejo de la energía, con lo cual, vale la pena hacer una exploración.
La supervisión y gestión del consumo de energía es bueno para la organización y para el medioambiente. Es un ganar en todos los sentidos. En los Estados Unidos, se requiere entre 30% y 40% de la electricidad generada para impulsar motores eléctricos industriales.
Incluso, una pequeña ganancia de eficiencia energética disminuiría significativamente la demanda agregada de energía, reduciendo el gasto de capital para construir más plantas de energía, el consumo de combustible fósil y las emisiones asociadas. Para la empresa, gastar menos en energía se traduce en un ahorro real en dólares. Además, al reducir la carga, el uso y desgaste de los activos industriales, se mejora la fiabilidad de fabricación, revalorizando su organización.
Esquemas del consumo de energía de máquinas industriales
Durante el ciclo de vida de un activo industrial, el consumo de energía de máquinas industriales es con frecuencia el mayor gasto. Algunos aspectos de los costes de energizar una máquina no pueden ser controlados, pero otros en cambio sí.
Veamos la economía de energizar un motor eléctrico de 200 caballos de fuerza. Suponiendo un factor de carga del 80% y un costo modesto de energía de 0,06$ por kilovatio hora (kWh), se requiere más de 57.000$ cada año para alimentar el motor, suponiendo 8000 horas de funcionamiento.
De hecho, hay motores que cuestan más, o menos, pero el punto es, que el coste para energizar el motor eléctrico es de aproximadamente 100 veces su precio de compra, asumiendo una vida útil de 10 años. Un recorte de entre 5% y 10% de este coste puede afectar profundamente en la línea de base.
Un 10% de mejora en eficiencia energética impulsa un extra de 5.700$ por debajo de la línea de base, y eso con un simple motor eléctrico de 200 hp. ¿Cómo se obtiene este ahorro? A continuación, serán enumerados algunos puntos para tu consideración. Algunos tienen efectos directos y positivos en fiabilidad de funcionamiento, además del obvio ahorro en los costes de energía.
Selecciona motores de alta eficiencia: Comparar el rendimiento entre placas de identificación de características técnicas. Los motores de alta eficiencia costarán más dinero por adelantado. No te deje llevar por los ahorros iniciales. Suponiendo que un motor eléctrico de eficiencia regular cuesta 5.000$ y utiliza un 10% más de energía que un motor de alta eficiencia, el cual podría costar más de 60,000$, todavía este último disminuiría los costes en términos de la tasa económica de retorno sobre el ciclo de vida de 10 años del motor eléctrico (suponiendo 8.000 horas por año de operación). El pago por adelantado de una prima de 50% para una alta eficiencia del motor eléctrico, produce una tasa interna de retorno del 229%. Eso es el equivalente de encontrar un banco que le pagara un interés del 229% al año por tus depósitos. Un 5% de eficiencia energética por la que se debe pagar 50% más, todavía tiene una tasa interna de retorno de 115%. Es fácil justificar esta inversión si se emplea el costo del ciclo de vida como herramienta de toma de decisiones.
Diseña trenes motrices para mejorar la eficiencia energética: Equivocarse al considerar las pérdidas energéticas en trenes de tracción mecánica puede afectar significativamente la factura de energía a causa de un solo activo industrial. Por supuesto, queremos motores eficientes, pero la mejora de la eficiencia del motor es solo la mitad de la batalla. Tenemos que gestionar también la eficiencia de los componentes accionados. Seleccionando diseños eficientes de cajas de cambios y acoples, entre otras acciones, se puede afectar sustancialmente el total de la cuenta de energía. Aplica al tren motriz entero los principios de precisión, balance, alineación, juego, resonancia y lubricación.
Administra el sistema eléctrico de manera integral: Si tu centro de control de motores tiene conexiones defectuosas, cableados degradados o sub dimensionados, la eficiencia energética estará comprometida en corto tiempo. Si los circuitos trabajan recalentados o se recalientan, la energía no se está distribuyendo eficientemente. Por otra parte, la fiabilidad del centro de control de motores y el motor pueden verse comprometidos. En el caso de corrientes parásitas, la alta acumulación de potencial también conduce a la erosión por descarga eléctrica, un desgaste del mecanismo al que se refiere como “estrías”. En conclusión, las pérdidas de energía comprometen la fiabilidad.
Operar en el rango ideal de carga: Usando nuestro ejemplo del motor eléctrico, si este opera por encima o por debajo de su rango de carga nominal, entonces produce una pobre eficiencia energética y disminuye su fiabilidad. Para la mayoría de los motores eléctricos la eficiencia energética disminuye precipitadamente cuando el motor es operado a menos del 40% de su carga nominal.
Optimizar reconstruir/reemplazar decisiones: Cuando un activo se desgasta, también se desajusta y pierde precisión, lo cual por supuesto resulta en derroche de energía. Conseguirás que al paso de unos pocos días, semanas o meses de servicio, resulte en altos costes de eficiencia energética.
Manejar el balance, alineación, ajuste y resonancia: El desbalanceo, desalineación, desajuste y resonancia, generan fricción mecánica. Esto potencia la generación de fricción, lo cual transforma la energía eléctrica en energía térmica y se debe pagar por ello. En algunas instancias la fricción es deseable, pero cuando es causada por una pérdida de precisión en el manejo del balanceo, desalineación, desajuste y resonancia, se está literalmente pagando por la energía requerida para incrementar el desgaste y reducir la fiabilidad de las máquinas. El mantenimiento de precisión da sus frutos, tanto en términos de fiabilidad como en gestión de la energía.
Emplear la lubricación de precisión: La selección de un lubricante con la viscosidad incorrecta puede afectar significativamente tanto al consumo de energía como a la fiabilidad. Si la viscosidad es muy baja, habrá fricción entre superficies. Si la viscosidad es muy alta, resultará en arrastre viscoso. Ambos desperdician energía. Un error común es el empleo de grasa multipropósito en los motores eléctricos. La viscosidad de la grasa es aproximadamente de 320 centistokes a 40 ºC. La mayoría de los motores eléctricos requieren grasa formulada usando una base aceite con una viscosidad de 100 a 150 cST a 40 ºC. La viscosidad extra reduce la eficiencia energética y compromete la fiabilidad del motor. Del mismo modo, los motores frecuentemente están sobre-engrasados, comprometiendo además la eficiencia energética y la fiabilidad.
Consumo de energía debido al monitoreo: Los cambios en la condición de los activos son frecuentemente puestos de manifiesto con la monitorización de la energía. Tradicionalmente empleamos el análisis de vibraciones, termografía y otras herramientas de monitoreo de condiciones para identificar y solucionar condiciones anormales en los activos industriales. Por definición, si una máquina comienza a vibrar o a recalentar, está utilizando más energía o transformando energía con reducción de eficiencia, por lo que monitorear la eficiencia energética es una actividad natural del monitoreo de condiciones. Por otra parte, es relativamente fácil de hacer y se puede realizar sobre una base continua. La monitorización de la energía también permite comparar la eficacia de diversos equipos y diseños de componentes, ayudando a tomar mejores decisiones en cuanto a diseño y adquisición de activos industriales que minimicen el coste del ciclo de vida de la propiedad y maximicen el rendimiento neto de los activos industriales.
La energía vale, y mucho
El monitoreo y gestión del consumo de la energía es un acierto. Ganar apenas 5% en mejora se puede traducir en un ahorro considerable para la organización. Si se está haciendo un mal manejo de los factores arriba mencionados, es posible 10%, 15% o más de merma. Porque esta energía desperdiciada, frecuentemente es convertida en calor y/o desplazamiento mecánico (vibración).
Una buena política de gestión de la energía y buena política de fiabilidad son aliados naturales. Hay muchos programas del gobierno que intentan motivar la conciencia energética, a menudo cubriendo toda (o parte de) la inversión requerida para mejorar la eficiencia energética.
Para recapitular: Se puede reducir la factura eléctrica, mejorar la fiabilidad, obtener apoyo económico del gobierno y practicar una buena ciudadanía medioambiental. ¿Qué te detiene? Comienza a monitorear y gestionar el consumo de energía hoy con el fin de minimizar el costo del ciclo de vida de tus propiedades.