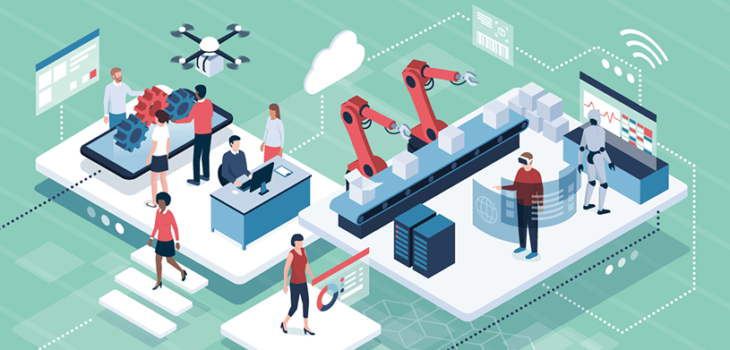
Guía para implantar la Industria 4.0 en cinco pasos
Es posible implantar la Industria 4.0 en una planta de fabricación en solo cinco pasos? Para empezar, la visión de la cuarta revolución industrial es una completa automatización de la creación de valor que involucra una producción totalmente automatizada en la cual la presencia humano no es indispensable.
De hecho, a la Industria 4.0 se le conoce como la fabricación con “luces apagadas”, debido a que puede operar mientras el personal duerme. Hoy en día esta es una práctica común en la fabricación de productos estándar, sin embargo, una vez que esto ya es posible, el siguiente objetivo no es otro que automatizar entornos de producción muchos más complejos.
Son muchas las empresas que comienzan con sus actividades de Industria 4.0 y se centran en la visión de la máxima automatización de la cadena de valor como estrella guía. Sin embargo, a menudo no están seguros de qué pasos deben tomar para lograr su objetivo.En este sentido, hemos querido hacer una guía para implantar la Industria 4.0 en cinco pasos, teniendo como base el funcionamiento de una planta que se ubica en la Industria 3.0 y el valor que estas aportan en la práctica. Por lo tanto, llegar a la fábrica de luces apagadas no es cuestión de simplemente presionar el interruptor, sino de un atenuador.
Implantar la Industria 4.0: Cinco pasos hacia el éxito de la fabricación automatizada
¿De qué forma se puede implementar la Industria 4.0 en una organización? Muchos responsables de planta están buscando optimizar la investigación o la estrategia para conseguirlo paso a paso, como hemos querido mostrarlo a través de esta publicación.
En primer término, implantar la Industria 4.0 bajo los conceptos básicos de fábrica inteligente depende de factores como:
- Los residuos y los retos de la producción,
- Los productos y sus variantes, y
- Los procesos de producción.
Pero hay pasos en los que, a menudo, se rompe un enfoque individual. Estos son los denominados “cinco pasos hacia el éxito” para allanar el camino para la Industria 4.0 para el sector manufacturero.
Paso 1: Conectividad de equipos y maquinarias
En realidad, esto es un shock para algunos, pero una fábrica inteligente necesita activos conectados. Esta es la base para utilizar datos para la automatización de la creación de valor. Para obtener mejores resultados, conecta máquinas, periféricos y otras fuentes de datos a una red común.
Una red común para los activos industriales y las bases de datos les permite comunicarse entre sí. Esto también se conoce como comunicación de máquina a máquina (M2M).
En la práctica, la conexión directa de activos va en contra del dogma de larga data. La mejor práctica de un controlador lógico programable PLC es una red de activos jerárquica. La fabricación tradicional conecta los activos a los PLC al sistema MES industrial. Esto ha demostrado ser beneficioso para la automatización del control, pero una estructura jerárquica no es lo suficientemente eficiente para manejar un tráfico elevado.
Sin embargo, cuando las máquinas se conectan a una red común, el valor proviene de:
- Tener un centro de control para todos los estados de las máquinas conectadas, y
- La posibilidad de acceso remoto a ellos.
Esto reduce el esfuerzo de mantener una visión general del estado de producción. Las tareas de programación simples o las verificaciones del historial de producción también se vuelven más fáciles. Solo la conexión de los activos hace uso exclusivo de la información del estado actual.
Paso 2: Adquisición de datos
Después de lograr la conectividad, viene la recopilación y el almacenamiento de datos de producción, una práctica ya común en la industria que permite la trazabilidad. Por tanto, los datos de producción y calidad se pueden archivar por producto. Esto es especialmente relevante en productos de seguridad y misión crítica.
Se pueden utilizar varias opciones para la recopilación de datos:
- En un búfer local en las máquinas individuales. Se trata de una práctica común.
- En un servidor de base de datos local. Este es el favorito de los clientes cautelosos, que quieren asegurarse de que ningún dato salga de la planta.
- En una infraestructura de nube global. Esto es algo que está ganando apoyo poco a poco también en las industrias tradicionales.
Una combinación inteligente de almacenamiento de datos logra la redundancia de datos. Esto se vuelve importante para reducir el riesgo de pérdida de datos. La optimización del almacenamiento también puede reducir la carga de la red y los requisitos totales de almacenamiento.
Es importante aclarar la seguridad del almacenamiento y transporte de datos. Especialmente cuando se manejan datos sensibles y confidenciales. Un ejemplo es la documentación de los pasos de montaje en automoción. Sus resultados se archivan junto con el identificador, el número de identificación del vehículo.
Paso 3: Visualización de datos de producción
Las aplicaciones de la Industria 4.0 se basan en datos. Pero no solo tienen como objetivo almacenarlo, sino también generar valor. Un primer uso de los datos es su visualización. Es una práctica común mostrar datos en paneles predefinidos.
Permiten al usuario filtrar los datos y el significado, los filtros y la clasificación les ayudan a obtener los primeros conocimientos, como:
- Los errores más comunes por máquina y por turno,
- La calidad total de la producción, y
- Los errores de máquina de disminución de calidad más comunes.
Pero al final, el valor que estos paneles aportan a la producción depende del usuario. Debido a que la herramienta de software no interpreta los datos, el experto humano debe hacerlo. Esto requiere un conocimiento profundo del proceso para llegar a las conclusiones correctas y mejorar la producción.
Paso 4: Analizar
¿Y si el software contuviera todo el conocimiento experto? Entonces podría apoyar a los operadores con información procesable inmediata. Este es el objetivo del paso 4, en el que también está trabajando la mayor parte de la industria.
Se trata de combinar los datos de activos disponibles con el conocimiento del proceso. Entonces, emulando cómo un experto usaría los datos para generar conocimientos.
El principal beneficio para la fabricación es el acceso inmediato y las 24 horas a la información. Esto mejora el tiempo de actividad, la productividad y la calidad de producción. Las tareas de optimización ahora pueden ser realizadas por empleados cualificados habituales.
Un ejemplo de uso de datos para generar conocimientos es el «mantenimiento predictivo». Esto programa las tareas de mantenimiento en función del estado de las máquinas, derivadas de los datos.
Paso 5: Automatización
Como último paso, el equipo es capaz de optimizarse y mantenerse a sí mismo. En este paso, vemos cómo una de las misiones de la Industria 4.0 cobra vida. La fábrica donde las máquinas apoyan toda la organización y la toma de decisiones. Los operadores de línea solo aprobarían tareas como cambios de parámetros. Entonces la máquina los realizaría por sí misma.
Aún así, un equipo de mantenimiento se encarga de los activos. Pero están coordinados por máquinas que solicitan servicio.