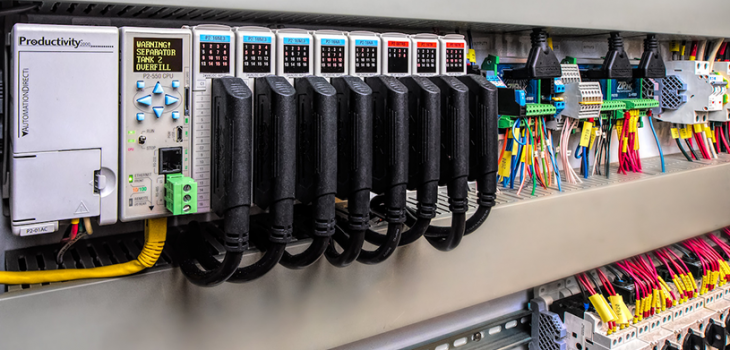
¿PLC, PAC o PC?: 16 mejores prácticas para elegir…
Elegir el controlador adecuado es fundamental para cualquier proyecto de automatización. Ya sea que se base en PLC, PAC o PC o en una combinación, tu plataforma de control debe funcionar de manera confiable durante muchos años.
La calidad, la funcionalidad, el coste, la facilidad de programación y mantenimiento, la capacidad de comunicarse y conectarse con múltiples dispositivos en la fábrica, así como la disponibilidad inmediata de soporte por parte del fabricante, son factores importantes en el proceso de selección.
En consecuencia, a continuación te ofrecemos las 16 mejores prácticas para elegir el controlador adecuado para tu proyecto de automatización:
Prueba de arranque. Al trabajar con un controlador, es importante conocer sus capacidades y si cumple con las necesidades de tu proyecto. No hay nada peor que estar a la mitad del proyecto, solo para descubrir que tu controlador no es capaz de hacer algo. Si el proyecto incluye algo que no has hecho antes, siempre prueba el proceso antes de comprometerlo en el proyecto.
No especifiques en exceso. No debes elegir el controlador específico demasiado pronto en la fase de diseño de un proyecto. La selección debe ocurrir solo después de que se complete la máquina inicial o el diseño conceptual de la automatización del proceso. Con demasiada frecuencia, un controlador sobreespecificado arroja innecesariamente los costes del proyecto de automatización. O peor aún, un controlador poco especificado puede resultar en esfuerzos de rediseño, compras adicionales y demoras en el cronograma.
Clarificar las interfaces. Si varias personas programan partes del código del PLC, dedica un tiempo, al inicio, para asegurarte de que las interfaces sean claras y que todos las entiendan.
Sin código enlatado. Cuando planifiques controles basados en PLC, si tus técnicos internos estarán involucrados en el mantenimiento y la actualización del nuevo sistema para futuras necesidades, no traigas “código enlatado”. Asegúrate de que tus técnicos tengan información sobre la estructura y la nomenclatura del programa. Los errores y los cambios son la norma con cualquier nuevo sistema de control, y encontrarás que tu instalación se recupera mucho más rápido después de un cambio tan importante en el equipo.
¿Podemos hablar? Una preocupación principal al implementar cualquier PLC son las comunicaciones. Esto se ha minimizado con la llegada de ODVA, pero aún puede ser un problema cuando se trata de algunos sensores o periféricos sofisticados. Elegir el controlador adecuado o una familia de PLC que tenga todos los módulos de comunicaciones de tipo de dispositivo es primordial. La mayoría de los PLC en el mercado pueden comunicarse en buses de dispositivos, pero no todos pueden acomodar todo tipo de Ethernet. Elige un PLC que pueda soportar todo sin mayor esfuerzo.
No todos los controladores o marcas son iguales. Consulta con personas con conocimientos en diferentes plataformas de hardware antes de especificar o seleccionar una determinada marca y modelo o incluso una plataforma. Demasiadas veces lo que se especifica no cumplirá con las expectativas del cliente. Eso deja brechas en lo que se oferta y requerirá cambios en el proyecto.
Puntos clave de verificación. Siempre que actualices un sistema o cambies de un controlador a otro, recuerda siempre verificar la fuente de alimentación del controlador, la memoria, el tipo de E/S, el tamaño y la disponibilidad en el panel. Verifica dos veces el propósito para el cual está destinado el controlador y siempre verifica cuidadosamente el número de modelo. Asegúrate de que el controlador tenga las características básicas que deseas, como bypass en línea, programación en línea, alarma gestión o control de circuito cerrado.
HMI primero. Al programar su proyecto, es mejor comenzar primero con la HMI. Si primero escribes el código de su programa, con frecuencia tendrás que volver a escribir su código para acomodar su HMI. Recuerda que crear una HMI de alto rendimiento es tener en cuenta que estás intentando capturar la esencia de la máquina o el proceso.
Carga de la CPU. Es importante considerar la carga de la CPU si el manejo de la comunicación es vital para la aplicación. La ejecución a la carga cíclica máxima dará como resultado una capacidad y tiempos de respuesta deficientes para la comunicación punto a punto y el servidor OPC. La carga cíclica máxima debe mantenerse por debajo del 65% y la carga cíclica estática por debajo del 60% en todas las condiciones. Incluso cargas cíclicas más bajas (30-40%) son deseables si es importante un alto rendimiento de comunicación.
El código. Pregúntales a las personas en la planta porqué corren como lo hacen. A veces, lo que podrías pensar es que la mala programación es realmente necesaria para ejecutar un proceso de manera óptima. Por otro lado, después de examinar el código, a menudo la gente piensa que un sistema se está ejecutando de una manera particular, pero la realidad es que no es así.
Software de documentos. El uso de controladores programables ofrece ventajas significativas sobre los dispositivos analógicos. Sin embargo, trae un nuevo conjunto de problemas. Primero, considera el control de múltiples parámetros del bloque de funciones. Es una buena práctica mantener el documento de control de configuración de software que resume todos los parámetros programables/ajustables en un solo lugar. Utilizarás este documento para cualquier evento de recuperación de desastres, incluidos los problemas de ciberseguridad o del ciclo de vida de la seguridad.
Piensa en el futuro. No elijas la opción más barata al instalar un PLC. Elegir el controlador adecuado requiere que pienses con cinco años de anticipación para acomodar la integración en la fábrica, las redes entre pares y el intercambio de datos entre controladores. El entorno moderno de la fábrica se está convirtiendo en una red de controladores integrados.
No compliques demasiado tu solución. Mantenlo lo más simple posible. No uses un sistema basado en PC cuando todo lo que necesita es un poco de control avanzado de E/S.
Experiencia previa. No uses un controlador para aplicaciones críticas en tu planta sin una experiencia exitosa de uso previo con un producto similar con los mismos componentes, firmware y software de nivel de revisión.
¿Son los micro PLC una opción? Los micro PLC con control flexible y “suficiente” pueden permitir a los OEM diferenciar sus equipos, particularmente en máquinas independientes. Al desarrollar una gama de máquinas independientes que utilizan la misma plataforma de controlador, los OEM pueden reducir el tiempo de diseño y reducir sus costos. Busque micro PLC que incluyen:
- Configuraciones de hardware flexibles, como USB, hasta seis puertos seriales y Ethernet para comunicaciones.
- Hasta tres ejes de movimiento incrustado.
- Plugins y expansión 2085 para E/S USB.
- Paquete de software de programación único que facilita la instalación, configuración, conectividad y mantenimiento.
Plataforma de control individual. Personalizar la selección de su controlador para cada aplicación puede parecer un movimiento inteligente, pero a veces vale la pena limitarse a una única plataforma de control. Examina tus requisitos y selecciona una plataforma capaz de manejar todas las necesidades actuales y futuras, desde las más simples hasta las más complejas. Seleccionar una única plataforma de control para todos tus requisitos de control de automatización, ya sea movimiento, robótica, control numérico, programa C o control de secuencia, puede reducir el inventario de piezas de repuesto, unificar los métodos de programación en todos los tipos de máquinas y simplificar los esfuerzos de capacitación y mantenimiento.
Fuente: Tecnología para la Industria