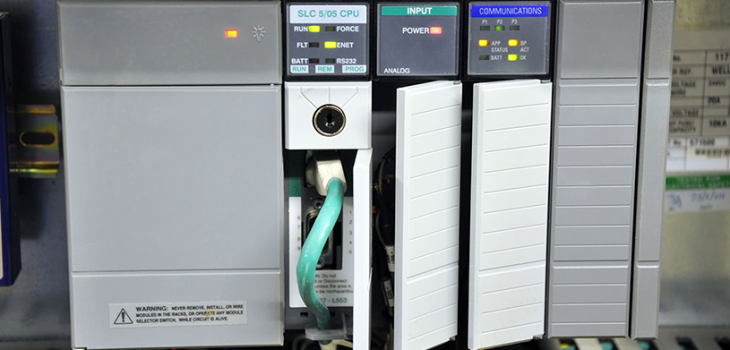
PLC vs. DCS: ¿Cuál es el sistema de control…
Muchos ingenieros nos hemos preguntado, al momento de poner en marcha un proyecto de automatización, ¿Cuál el sistema de control más adecuado? Durante la última década, la funcionalidad de diferentes sistemas de control se ha fusionado. Los controladores lógicos programables (PLC) ahora tienen capacidades que antes solo se encontraban en los sistemas de control distribuido (DCS), mientras que un DCS puede manejar muchas funciones que antes se consideraban más apropiadas para los PLC.
Entonces: ¿Cuál es la diferencia entre los dos enfoques de control? ¿Dónde está la línea divisoria? ¿Todavía hay razones para elegir uno sobre el otro? Los PLC crecieron como reemplazos para múltiples relés y se utilizan principalmente para controlar procesos de fabricación discretos y equipos independientes. Si se requiere la integración con otro equipo, el usuario o su integrador de sistemas generalmente tiene que hacerlo, conectando las interfaces hombre-máquina (HMI) y otros dispositivos de control según sea necesario. El DCS, por otro lado, fue desarrollado para reemplazar los controladores PID y se encuentra con mayor frecuencia en procesos de producción por lotes y continuos, especialmente aquellos que requieren medidas de control avanzadas en los cuales el proveedor maneja la integración del sistema, y las HMI son integrales. A medida que los usuarios exigían más información de producción, los PLC ganaron poder de procesamiento y las redes se hicieron comunes. Los sistemas de control basados en PLC comenzaron a funcionar como un mini-DCS. Al mismo tiempo, el DCS se hibridó para incorporar PLC y PC para controlar ciertas funciones y proporcionar servicios de informes. El DCS supervisa todo el proceso, al igual que el director de una orquesta. Los protocolos, como OPC, han facilitado las interacciones entre los dos sistemas de control. Como los PLC son menos costosos y ahora pueden funcionar como un sistema de control distribuido, ¿No tendría sentido convertir todo en PLC? La respuesta, como la mayoría de las cosas en el mundo de la automatización industrial, es que depende de las necesidades de su aplicación y aquí hay seis factores clave a considerar:
Tiempo de respuesta Los PLC son rápidos, sin duda. Los tiempos de respuesta de una décima de segundo hacen que el PLC sea un controlador ideal para acciones casi en tiempo real, como un apagado de seguridad o un control de disparo. Un DCS tarda mucho más en procesar datos, por lo que no es la solución correcta cuando los tiempos de respuesta son críticos. De hecho, los sistemas de seguridad requieren un controlador separado.
Escalabilidad Un PLC solo puede manejar unos pocos miles de puntos de E/S o menos. Simplemente no es tan escalable como un DCS, que puede manejar miles de puntos de E/S y acomodar más fácilmente nuevos equipos, mejoras de procesos e integración de datos. Si necesitas un control de proceso avanzado y tienes una instalación grande o un proceso que se extiende en un área geográfica amplia con miles de puntos de E/S, un DCS tiene más sentido.
Redundancia Otro problema con los PLC es la redundancia. Si necesitas energía o E/S tolerantes a fallas, no intentes forzar esos requisitos en un sistema de control basado en PLC. Simplemente terminará aumentando los costos para igualar o superar los de un DCS.
Complejidad La naturaleza compleja de muchos procesos de producción continua, como el petróleo y el gas, el tratamiento del agua y el procesamiento químico, continúa requiriendo las capacidades avanzadas de control de procesos del DCS. Otros, como la automatización de procesos en plantas de pulpa y papel, tienden hacia el control basado en PLC.
Cambios frecuentes en el proceso
Los PLC se aplican mejor a un proceso dedicado que no cambia con frecuencia. Si tu proceso es complejo y requiere ajustes frecuentes o debe agregar y analizar una gran cantidad de datos, un DCS suele ser la mejor solución. Por supuesto, la flexibilidad misma de un sistema DCS también lo hace mucho más vulnerable a la “intromisión» de los operadores que pueden causar paradas espurias.
Apoyo del vendedor Los proveedores de DCS generalmente requieren que los usuarios los empleen para proporcionar servicios de integración e implementar cambios en el proceso. Los integradores de sistemas realizan funciones similares para sistemas basados en PLC. También se ha vuelto común que los proveedores de PLC ofrezcan servicios de soporte a través de su red de socios integradores de sistemas.
El control del proceso se ha vuelto cada vez más complejo. Es difícil para cualquier persona saber todo acerca de estos sofisticados sistemas de control, lo que aumenta la necesidad de soporte de proveedores.
Los fabricantes también continúan reduciendo el personal de la fábrica y una generación de personal experimentado en control de procesos ha comenzado a retirarse. Como resultado, la calidad del soporte se ha convertido en un factor crítico en la selección de proveedores.
Fuente: Tecnología para la Industria