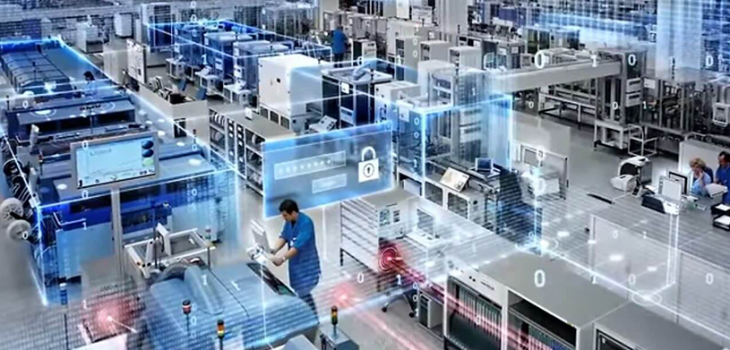
Uso de datos para impulsar la productividad de la…
¿Qué nos impide aumentar la productividad en nuestras plantas al siguiente nivel? Durante una presentación reciente sobre Industria 4.0 y IIoT, me hicieron esta pregunta.
Lo más importante, en mi opinión, que nos impide aumentar la productividad al siguiente nivel es la falta de DATOS. Específicamente, datos sobre los sistemas y los procesos.
Desde el principio de los tiempos, hemos tenido hambre de eficiencia. Mientras que el hombre primitivo inventó métodos más eficientes para cazar y sobrevivir, hoy estamos buscando formas de producir de manera más eficiente en nuestras plantas con un mínimo o cero desperdicio. Después de agotar todas las vías para operaciones lean en los procedimientos de la planta y nuestras actividades cotidianas, ahora estamos viendo cómo podemos recuperarnos de un tiempo de paro inesperado rápidamente. Estoy seguro de que en el futuro buscaremos información sobre cómo podemos evitar el tiempo de inactividad por completo.
Hay muchas razones para el tiempo de paro. Solo algunos ejemplos:
- Falta de disponibilidad de mano de obra, algo que podríamos estar experimentando en estos días, cuando la pandemia de COVID-19 ha reducido algunas fuerzas laborales.
- Falta de disponibilidad de materias primas.
- Falta de disponibilidad de refacciones.
- Falta de disponibilidad de activos.
- Fallas en máquinas/componentes.
En esta lista, las dos primeras razones están más allá del alcance de las intenciones de este blog y, francamente, están fuera de control desde el punto de vista de la producción.
Sin embargo, las siguientes dos razones están relacionadas con el proceso y la última se basa únicamente en las elecciones que tomamos. Estas tres razones, hasta cierto punto, pueden reducirse o eliminarse.
Si el tiempo de paro está relacionado con el proceso, podemos aprender de ellos y mejorar nuestros procesos con las llamadas iniciativas de mejora continua. Solo podemos hacer estas mejoras continuas basadas en factores observables (también conocidos como datos) y no podemos mejorar nuestros procesos basados en especulaciones. Bueno, no debería decir “no se puede”, pero será más como una casualidad o suerte. Es correcto para decir “¡lo que no se puede medir, no se puede mejorar!”
Un buen ejemplo para elaborar mi punto es el cambio en la planta para producir un producto diferente. A menos que exista un buen proceso para garantizar que todos los puntos de cambio se aborden correctamente y que todas las partes de cambio se instalen y reemplacen correctamente, el tiempo de cambio podría y probablemente conducirá a enormes cantidades de pérdida de productividad. En segundo lugar, si estos procesos se realizan de forma manual y no automatizada, eso también es una pérdida de productividad o, como me gusta decir, un área de mejora continua para aumentar la productividad en función de hechos observables. A veces, tomamos estos cambios manuales como una realidad e incorporamos ese tiempo requerido como parte del tiempo de inactividad “planificado”. Por supuesto, si realiza cambios una vez al año, puede ser rentable mantener el proceso manual incluso en la situación actual. Pero, si su planta tiene múltiples producciones de lotes pequeños por día o por semana, entonces la automatización de los cambios podría aumentar significativamente la productividad. El análisis de costo-beneficio debería ayudar a demostrar si es una mejora continua o no.
Los activos son una parte importante de la ecuación para operaciones sin problemas. Un ejemplo serían los moldes en la planta de troquelado o las herramientas de desbarbado y de corte en las plantas metalúrgicas. Si las plantas no tienen visibilidad o trazabilidad de estos activos importantes para su ubicación, estado o forma, podría generar un tiempo de paro considerable. Los datos de calibración de estas herramientas o el número de piezas producidas con la herramienta también son datos importantes que deben mantenerse para operaciones eficientes. Nuevamente, estos son datos sobre el sistema y la integración de estas iniciativas de trazabilidad en la infraestructura existente.
Las fallas en máquinas o componentes pueden causar un tiempo de inactividad severo y, a menudo, se consideran inevitables. Abordamos estas fallas en un enfoque de dos pasos. Primero, buscamos el problema cuando no es obvio, y dos, encontramos la pieza de repuesto en el almacén para cambiarlo rápidamente. Y, como mejora del proceso, programamos el mantenimiento preventivo para inspeccionar, lubricar y reemplazar piezas en nuestro tiempo de inactividad planificado regularmente.
El mantenimiento preventivo generalmente se programa en función de la tasa teórica de falla. Esta es una buena medida, especialmente para componentes mecánicos, pero el mantenimiento predictivo o basado en la condición generalmente produce mayores rendimientos de productividad y ayuda a mantener las plantas funcionando sin problemas. Nuevamente, el mantenimiento predictivo se basa en datos sobre la condición del sistema o componentes. Entonces, ¿dónde están estos datos y cómo llegamos a ellos?
La estandarización de las interfaces es otro componente importante para impulsar la productividad.